Neste artigo será abordado quais os tipos de manutenção industrial são utilizadas nos dias de hoje e como elas são caracterizadas. No Brasil e no mundo a manutenção industrial é extremamente necessária para a boa operação do maquinário e da eficiência, tanto de produção quanto de recursos.
MANUTENÇÃO CORRETIVA
A manutenção corretiva é a atuação para a correção da falha ou do desempenho menor que o esperado. Ao atuar em um equipamento que apresenta um defeito ou um desempenho diferente do esperado estamos realizando manutenção corretiva. Sendo assim, a manutenção corretiva não é, necessariamente, a manutenção de emergência.
Podemos ter duas condições específicas que levam à manutenção corretiva:
- O equipamento apresenta desempenho deficiente.
- ∙Ocorrência de falha.
Então a principal função da Manutenção Corretiva é Corrigir ou Restaurar as condições de funcionamento do equipamento ou sistema.
Podemos dividir a Manutenção Corretiva em duas classes:
- Manutenção Corretiva Não Planejada.
- Manutenção Corretiva Planejada.
MANUTENÇÃO CORRETIVA NÃO PLANEJADA
É a correção da falha de maneira aleatória, caracterizando-se pela atuação da manutenção em um fato já ocorrido, seja este uma falha ou um desempenho menor que o esperado. Não há tempo para a preparação do serviço. Infelizmente ainda é mais praticado do que se deveria.
Normalmente a manutenção corretiva não planejada implica em altos custos, visto que a quebra inesperada pode acarretar perdas de produção, perda na qualidade do produto e elevados custos indiretos de manutenção.
Além disso, quebras aleatórias podem ter conseqüências bastante graves para o equipamento, isto é, a extensão dos danos pode ser bem maior. Em plantas industriais de processo contínuo como, por exemplo: petróleo, petroquímico, cimento dentre outras, estão envolvidas no seu processo elevadas pressões, temperaturas, vazões, ou seja, a quantidade de energia desenvolvida no processo é considerável. Interromper tais processos de forma abrupta para reparar um determinado equipamento compromete a qualidade de outros que vinham operando em condições regulares, levando-os a colapsos após a partida ou a redução da produção da planta. Exemplo típico é o surgimento de vibração em grandes máquinas que apresentavam funcionamento suave antes da ocorrência.
No caso de uma empresa ter a maior parte de sua manutenção corretiva na classe de não planejada, o seu departamento de manutenção acaba sendo comandado pelos equipamentos e o desempenho da empresa, certamente, não estará adequado às necessidades de competitividade atuais.
MANUTENÇÃO CORRETIVA PLANEJADA
A manutenção corretiva é a correção do desempenho menor que o esperado ou da falha, por decisão gerencial, isto é, pela atuação em função de acompanhamento preditivo ou pela decisão de operar o equipamento até a sua quebra.
Visto que um trabalho planejado é sempre mais barato, mais rápido e mais seguro do que um trabalho não planejado, será sempre de melhor qualidade. A característica principal da manutenção corretiva planejada é a função da qualidade da informação fornecida pelo acompanhamento do equipamento.
Mesmo que a decisão gerencial seja de deixar o equipamento funcionar até a quebra, essa é uma decisão conhecida e algum planejamento pode ser feito quando a falha ocorrer. Podemos citar, por exemplo, substituir o equipamento por outro idêntico, ter um Kit de reparo rápido.
A adoção de uma política desse tipo de manutenção pode se originar de vários fatores:
- Melhor planejamento dos serviços.
- Possibilidade de compatibilizar a necessidade da intervenção com os interesses da produção.
- Aspectos relacionados com a segurança-falha não provocam nenhuma situação de risco para o pessoal ou para a instalação.
- Garantia de equipamentos sobressalentes, equipamentos e ferramental.
- Ter recursos humanos com a tecnologia necessária para a execução dos serviços, que podem também ser terceirizados.
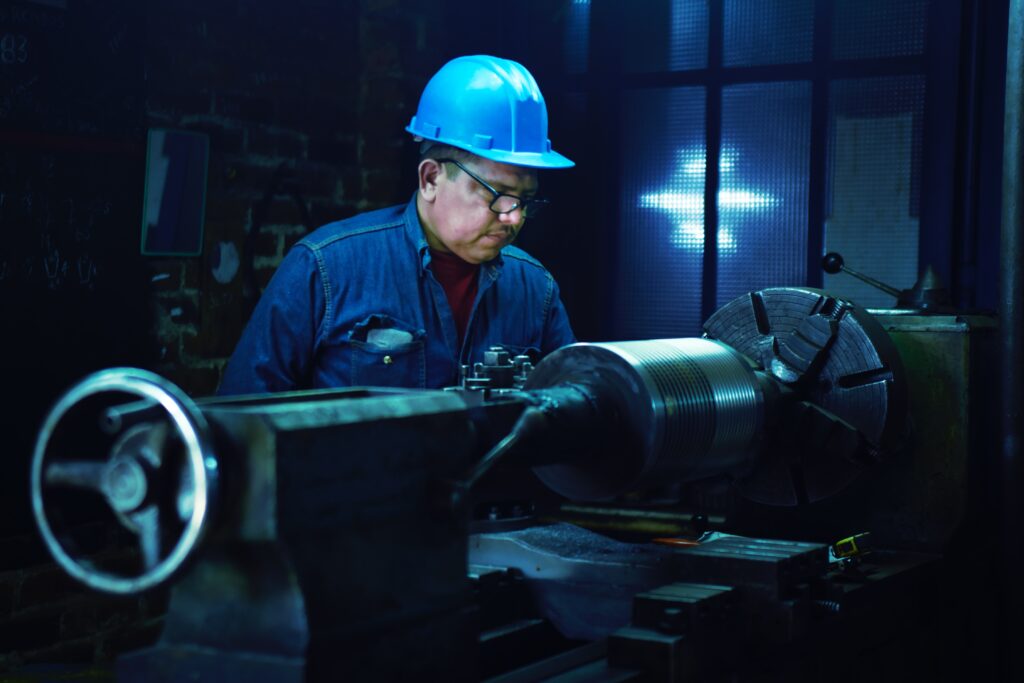
MANUTENÇÃO PREVENTIVA
Manutenção Preventiva é a atuação realizada de forma a reduzir ou evitar a falha ou queda no desempenho, obedecendo a um plano previamente elaborado, baseado em INTERVALOS definidos de TEMPO.
Inversamente à política de Manutenção Corretiva, a Manutenção Preventiva procura obstinadamente evitar a ocorrência de falhas, ou seja, procura prevenir. Em determinados setores, como na aviação, a adoção de manutenção preventiva é imperativa para determinados sistemas ou componentes, pois o fator segurança se sobrepõe aos demais.
Como nem sempre fabricantes fornecem dados precisos para a adoção nos planos de manutenção preventiva, além das condições operacionais e ambientais terem influência de modo significativo na expectativa de degradação dos equipamentos, a definição de periodicidade e substituição deve ser estipulada para cada instalação ou no máximo plantas similares operando também em condições similares.
Isso leva à existência de duas situações distintas na fase inicial de operação:
a) Ocorrência de falhas antes de completar o período estimado, pelo mantenedor, para intervenção.
b) Abertura do equipamento/reposição de componentes prematuramente. Evidentemente, ao longo da vida útil do equipamento não pode ser detectada a falha entre duas intervenções preventivas, o que, obviamente, implica uma ação corretiva.
Os seguintes fatores devem ser levados em consideração para adoção de uma política de manutenção preventiva:
- Quando não é possível a manutenção preditiva.
- Aspectos relacionados com a segurança pessoal ou da instalação que tornam necessária a intervenção, normalmente para substituição de componentes.
- Por oportunidade em equipamentos críticos de difícil liberação operacional.
- Riscos de agressão ao meio ambiente.
- Em sistemas complexos e/ou de operação contínua. Ex. petroquímica, siderúrgica, indústria automobilística, etc.
A manutenção preventiva será tanto mais conveniente quanto maior for a simplicidade na reposição; quantos mais altos forem os custos de falhas; quanto mais falhas prejudicarem a produção e quanto maiores forem as implicações das falhas na segurança pessoal e operacional.
MANUTENÇÃO PREDITIVA
A Manutenção Preditiva, também conhecida por Manutenção Sob Condição ou Manutenção com Base no Estado do Equipamento, pode ser definida da seguinte forma:
Manutenção Preditiva é a atuação realizada com base em modificação de parâmetro de CONDIÇÃO ou DESEMPENHO, cujo acompanhamento obedece a uma sistemática.
A Manutenção Preditiva é a primeira grande quebra de paradigma na Manutenção e tanto mais se intensifica quanto mais o conhecimento tecnológico desenvolve equipamentos que permitam avaliação confiável das instalações e sistemas operacionais em funcionamento.
Seu objetivo é prevenir falhas nos equipamentos ou sistemas através de acompanhamento de parâmetros diversos, permitindo a operação contínua do equipamento pelo maior tempo possível. Na realidade o tempo associado à Manutenção Preditiva é o de predizer as condições dos equipamentos. Ou seja, a Manutenção Preditiva dá preferência à disponibilidade, à medida que não promove a intervenção nos equipamentos ou sistemas, pois as medições e verificações são efetuadas com o equipamento produzindo.
Quando o grau de degradação se aproxima ou atinge o limite previamente
estabelecido, é tomada a decisão de intervenção. Normalmente esse tipo de acompanhamento permite a preparação prévia do serviço, além de outras decisões e alternativas relacionadas com a produção. De forma mais direta, podemos dizer que a Manutenção Preditiva prediz as condições dos equipamentos e quando a intervenção é decidida o que se faz, na realidade, é uma manutenção corretiva planejada.
As condições básicas para adotar a Manutenção Preditiva são as seguintes:
- O equipamento, sistema ou instalação devem permitir algum tipo de monitoramento/medição.
- O equipamento, sistema ou instalação devem merecer esse tipo de ação em função dos custos envolvidos.
- As falhas devem ser oriundas de causas que possam ser monitoradas e ter sua progressão acompanhada.
- Seja estabelecido um programa de acompanhamento, análise e diagnóstico, sistematizado.
Os fatores indicados para análise da adoção de política de Manutenção Preditiva são os seguintes:
- Aspectos relacionados com a segurança pessoal e operacional.
- Redução de custos pelo acompanhamento constante das condições dos equipamentos, evitando intervenções desnecessárias.
- Manter os equipamentos operando, de modo seguro, por mais tempo.
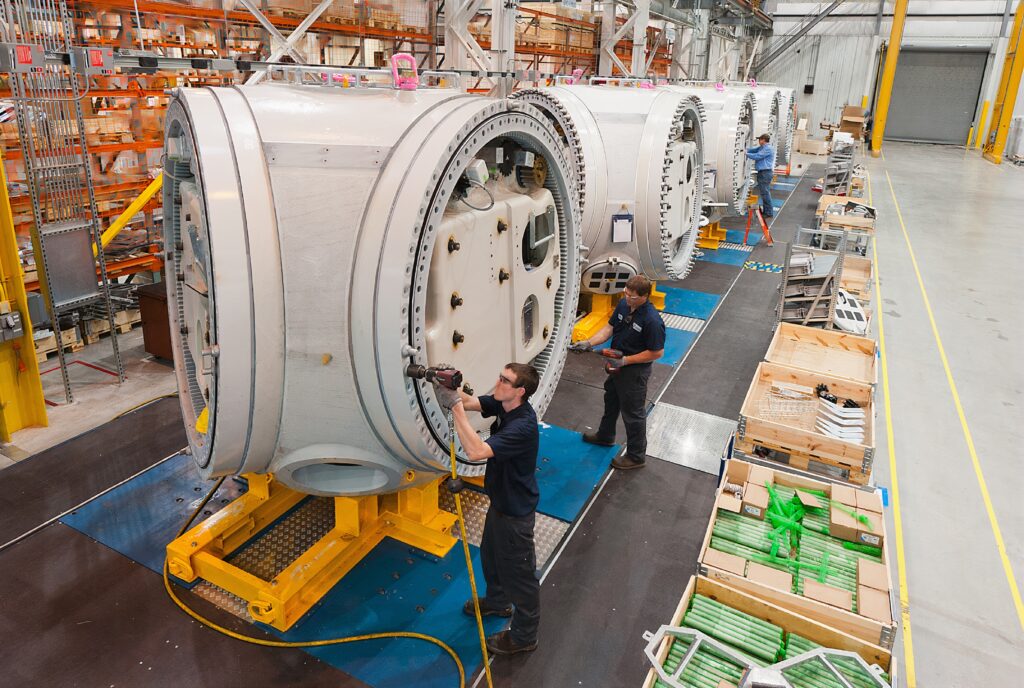
MANUTENÇÃO DETECTIVA
A Manutenção Detectiva começou a ser mencionada na literatura a partir da década de 90. Sua denominação Detectiva está ligada à palavra Detectar em inglês Detective Maintence. Pode ser definida da seguinte forma:
Manutenção Detctiva é a atuação efetuada em sistemas de produção buscando detectar FALHAS OCULTAS ou não perceptíveis ao pessoal de operação e manutenção.
Desse modo, tarefas executadas para verificar se um sistema de proteção ainda está funcionando representam a Manutenção Detectiva. Um exemplo simples e objetivo é o botão de teste de lâmpadas de sinalização e alarme em painéis.
A identificação de falhas ocultas é primordial para garantir a confiabilidade. Em sistemas complexos essas ações só devem ser levadas a efeito por pessoas da área de manutenção, com treinamento e habilitação para tal, assessorado pelo pessoal de operação.
É cada vez maior a utilização de computadores digitais e instrumentação e controle de processo nos mais diversos tipos de plantas industriais.
“São sistemas de aquisição de dados, controladores lógicos programáveis, Sistemas Digitais de Controle Distribuído – SDCD, multi- loops com computador supervisório e outra infinidade de arquiteturas de controle somente possíveis com o advento de computadores de processo. Sistema de shut-down ou sistema trip garantem a segurança do processo quando esse sai de sua faixa de operação segura. Esses sistemas de segurança são independentes dos sistemas de controle utilizados para otimização da produção. Equipamentos eletrônicos programáveis estão sendo utilizados para essas aplicações.”
Enquanto a escolha deste ou daquele sistema ou de determinados tipos de componentes é discutida pelos especialistas com um enfoque centrado basicamente na confiabilidade, são importantes que estejam bastante claras as seguintes particularidades:
- Os sistemas de trip ou shut-down são a última barreira entre a integridade e a falha. Graças a eles as máquinas, equipamentos, instalações e até mesmo plantas inteiras estão protegidos contra falhas e suas consequências menores, maiores ou catastróficas.
- Esses sistemas são projetados para atuar automaticamente na iminência de desvios que possam comprometer as máquinas, a produção, a segurança no seu aspecto global ou o meio ambiente.
- Os componentes dos sistemas de trip ou shut-down, como qualquer componente, também apresenta falha.
- As falhas desses componentes e, em última análise, do sistema de proteção, podem acarretar dois problemas:
✔ Não atuação.
✔ Atuação indevida.
A não atuação de um sistema trip ou shut-down é algo que jamais passa despercebido. É evidente que existem situações onde é possível contornar ou fazer um acompanhamento, mas em outras isso é definitivamente impossível.
Fica evidente que a mudança do status quo é ter o domínio da situação. Essa modificação é obtida com a Manutenção Detectiva. Na Manutenção Detectiva, especialistas fazem verificações no sistema, sem tirá-lo de operação, capazes de detectar falhas ocultas, e preferencialmente podem corrigir a situação, mantendo o sistema operando.
Quer saber como podemos te ajudar? Fale agora mesmo com um especialista da Solidus.